فولاد spk در استاندارد AISI تحت عنوان فولاد D3 نیز شناخته میشود. فولاد سرد کار D3 به دلیل حجم بالایی از کاربیدهای سخت موجود در زمینه فولاد، دارای مقاومت بالایی در مقابل سایش بوده که آنها را در گروه فولادهای ابزار قرار میدهد. همچنین از دیگر ویژگیهای آن میتوان به چقرمگی متوسط، پایداری ابعادی، استحکام فشاری اشاره کرد.
به طور معمول این نوع فولاد در محیط روغن کوئنچ میشود اما گاهی نیز میتوان در خلاء آن را خنک کرد اما در هر صورت تمایل زیادی به تردی پس از عملیات حرارتی از خود نشان میدهد.
ف
اخت و عملیات حرارتی فولاد SPK
1- عملیات فورجینگ
جهت انجام عملیات فورجینگ بر روی فولاد SPK ابتدا باید عملیات پیشگرم کردن در بازه دمایی 900-950 درجه سانتیگراد انجام شود و سپس دما را به حدود 1050-1100 درجه سانتیگراد رساند و نمونه باید به طور یکنواخت حرارت داده شود. در نتیجه این فولاد با افزایش دما به مراتب سخت میشود. باید توجه داشت که ضربات اولیه توسط چکش باید چندان محکم نبوده و همچنین اجازه داده نشود تا قبل از اینکه تغییر شکل در فولاد اتفاق افتند، دما به زیر 1020 درجه کاهش پیدا کند. همچنین فورج نهایی نباید در زیر 900 درجه سانتیگراد انجام شود.
اگر واژه فورجینگ برای شما مبهم است، پیشنهاد میکنیم مقاله فورجینگ چیست را مطالعه کنید.
2- عملیات آنیلینگ
فولادهای ابزار کارسرد نظیر SPK در شرایط آنیل ارائه میشوند تا قابلیت ماشینکاری نیز داشته باشند. ضمن اینکه اگر قرار باشد از این فولاد جهت فورجینگ و یا سختکاری استفاده شود، عملیات آنیل روی آن انجام نخواهد شد.
در آنیلینگ، حرارت به آهستگی و یکنواخت تا حدود 900 درجه سانتیگراد افزایش مییابد و سپس به مدت 3 الی 4 ساعت در کوره تا رسیدن به دمای اتاق سرد میشود. سپس دوباره تا دمای حدود 800-1040 درجه حرارت داده شده و مجددا به مدت 3 تا 4 ساعت در کوره تا رسیدن به دمای اتاق سرد شود.
3- تنش زدایی
وقتی ابزارها نیاز به ماشینکاری زیاد، سنگزنی و یا عملیات مشابه پیدا کنند، تنشهای داخلی ایجاد شده در حین این فرآیندها قابلیت تغییر شکل یافتن را قبل از سختکاری در آنها به حداقل میرساند.
به همین دلیل این ابزارها بعد از ماشینکاری نیاز به تنشزدایی پیدا میکنند که برای این منظور آنها را تا دمایی حدود 600-650 درجه سانتیگراد حرارت داده و سپس در هوا و یا کوره خنک میکنند.
4- عملیات سختکاری
ترجبح داده میشود که فولادهای ابزار کارسرد نظیر SPK در اتمسفر کنترل شده حرارت داده شوند که اتمسفر احیایی از این نظر مطلوب میباشد. پیش گرمی معادل 750-800 درجه سانتیگراد اعمال شده و به ماده مورد نظر اجازه داده میشود برای مدت زمانی در این وضعیت باقی بماند.
سپس با توجه به نوع محیط خنک کننده، برای خنک سازی در هوا به دمای 1000 درجه و برای خنک سازی در روغن به دمای 980 درجه سانتیگراد برده میشود. در این رابطه، به ازای هر 25 میلیمتر از ضخامت نمونه، باید حدود 25 دقیقه در دمای یاد شده قرار گیرد. ضمن اینکه باید توجه داشت که دمای فرآیند جهت سختکاری هیچگاه نباید از 1020درجه سانتیگراد تجاوز کند.
5- عملیات مارتمپرینگ
مارتمپرینگ نوع دیگیری از فرآیند سختکاری است که در صورت وجود حمام نمک به عنوان محیط خنککننده مورد استفاده قرار میگیرد. با این روش، تنشهای داخلی، اعوجاجها و احتمال ترک برداستن نمونه بعد از کوئنچ کردن کاهش مییابد.
پیش گرم به اندازه 300- 400 درجه سانتیگراد و سپس حرارتدهی تا بازه 950 – 980 درجه و سپس نگهداری در حمام نمک به مدت 10 دقیقه به ازای هر 25 میلیمتر از ضخامت نمونه نیاز است. سپس مرحلهی مارکوئنچینگ در حمام نمک در دمای 230 – 250 درجه سانتیگراد و نگهداری به مدت 5 دقیقه به ازای هر 25 میلیمتر از ضخامت نمونه برای فولاد SPK به کار گرفته میشود و سردسازی نهایی نیز در هوا انجام میشود و سپس عملیات تمپر باید انجام شود.
6- عملیات تمپرینگ
برای فولادهای SPK، دو مرحله عملیات تمپر توصیه شده است. تمپرینگ باید بلافاصله پس از عملیات مارتمپرینگ و درحالی که فولاد مورد نظر هنوز گرم است، انجام شود. با توجه به نیازمندیهای شرایط سرویس، دمای مناسب جهت تمپر انتخاب میشود و حرارت به صورت آهسته و یکنواخت به قطعه اعمال میشود. وقتی نمونه به دمای مورد نظر رسید، نمونه باید به ازای هر 25 میلیمتر از ضخامت، به مدت 1 ساعت در آن شرایط باقی بماند. سپس دوباره همین سیکل تکرار میشود.
تاثیرات عملیات حرارتی بر ریزساختار فولاد SPK
در طول فرآیند انجماد این نوع فولاد، در ابتدا دندریتهای آستنیت جوانه میزنند. کسر حجمی این دندریتها با کاهش دما افزایش یافته و مذاب باقیمانده از کربن و کروم اشباع میشود. در مرحله پایانی فرایند انجماد، در دمای یوتکتیک، مذاب باقیمانده به کاربیدهای کروم با فرمول Cr_7 C_3 و مورفولوژی آستنیت و فریت به صورت اسکلتی تبدیل میشود.
تحت چنین شرایطی به دلیل جدایش بین کربن و کروم، مقدار هر یک از این عناصر در مناطق مرکزی هر قطعه کمتر از مقادیر آنها در مناطق بیرونی خواهد بود. بنابراین سختی بالایی در مرکز قطعه حاصل نخواهد شد.
در همین رابطه گزارش شده است که فرآیندهای نیمه جامد و سرعتهای سرمایش بالا میتوانند ریزساختار مناسبی از فولادهای SPK و به طور کلی فولادهای سری D طبق استاندارد AISI را به دست دهند.
کاربید کروم در فولادهای ابزار سری D شامل ترکیبات M_3 C و M_7 C_3 میشوند. سختی ویکرز برای ترکیب M_3 C در حدود 1060 – 1240 با حداکثر مقدار کروم 25 درصد و برای ترکیب M_7 C_3 سختی ویکرز معادل 1500 – 1800 با حداکثر مقدار کروم 50 درصد گزارش شده است.
با انجام عملیات حرارتی بر روی فولاد SPK، کاربیدهای M_7 C_3 در نمونه استاندارد به کاربیدهای MC که دارای ترکیب شیمیایی (NbTi)C میباشند تغییر پیدا کرده که در نتیجه آن، سختی ویکرز از 1075 – 1171 به مقدار 2125 در کاربیدهای جدید میرسد.
در طول همگن سازی نیز کاربیدهای MC در دمای کمتر از 1200 درجه سانتیگراد پایدار بوده و در زمینه حل نمیشوند در حالیکه کاربیدهای کروم به صورت جزیی در زمینه حل خواهند شد. همچنین زمان و دمای بهینه جهت همگنسازی به ترتیب معادل 30 دقیقه و بازه دمایی 1000 – 1100 درجه سانتیگراد گزارش شده است. ضمن اینکه سختی نمونه های حاصل از عملیات همگنسازی و آنیل به مقدار کمتر از 25 HRC خواهد رسید.
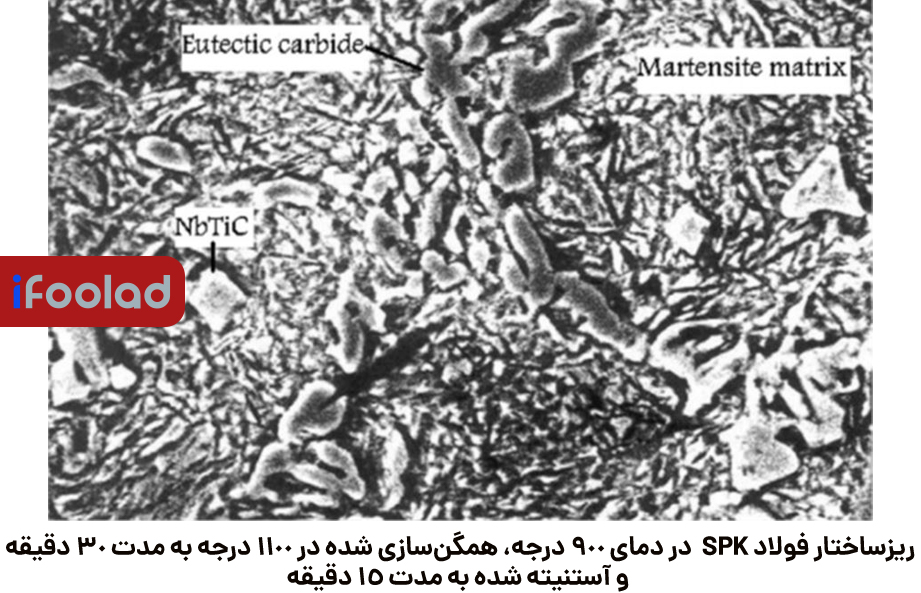
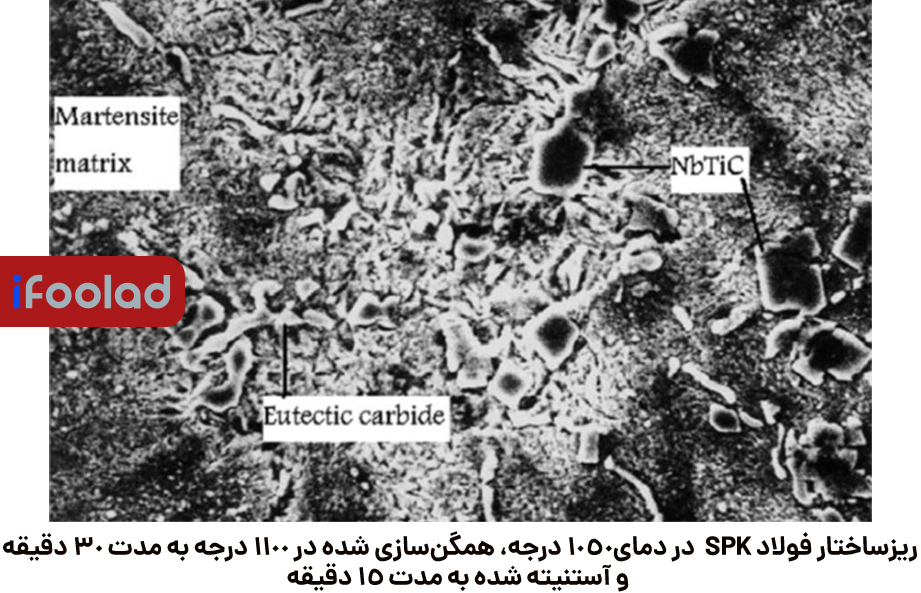
تاثیرات عملیات حرارتی بر خواص مکانیکی فولاد SPK
اعمال عملیات حرارتی بر روی فولاد SPK باعث تبدیل نیمی از کاربیدهای کروم به صورت کاربیدهای نیوبیوم و تیتانیم با فرم (NbTi)C شده و خواص مکانیکی این فولاد را تحت تاثیر قرار میدهد به گونهای که در طول فرآیند تمپر، سختی ثانویه در دمای 500 درجه در نمونهای که در دمای 1050 درجه سانیگراد آستنیته شده اتفاق میافتد.
بعد از عملیات تمپر در دمای 300 درجه سانتیگراد، سختی فولادهای اصلاح شده (جایگزین شدن کاربیدهای جدید) به مقدار 1 HRC بیشتر از حالت قبل از اصلاح گزارش شده است. ضمن اینکه در این دما، استحکام خمشی به میزان 89 درصد نسبت به حالت اولیه بهبود یافته است.
طبق نتایج به دست آمده، به غیر از قطعاتی که در 1050 درجه سانتیگراد آستنیته شدهاند، سایر قطعات با افزایش درجه حرارت تمپر، مقدار سختی آنها کاهش یافته است. این امر به دلیل مکانیزمهایی است که در طی فرآیند تمپرینگ رخ داده است که در این رابطه میتوان به تجزیه مارتنزیت پر کربن به مارتنزیت کم کربن، تبدیل آستنیت باقیمانده به فریت و کاربید و همچنین تبدیل مارتنزیت کم کربن به فریت و کاربید اشاره کرد.
ضمن اینکه روند کاهش سختی نمونهها تا دمای 300 درجه سانتیگراد آهسته بوده و در دمای بالای 400 درجه سانتیگراد روند سریعتری پیدا کرده که ناشی از رسوب مقادیر زیادی کاربید بوده و به دنبال آن پارامتر شبکه مارتنزیت و نیز کرنشهای شبکهای کاهش خواهند یافت.
به علاوه، بررسی تغییرات استحکام خمشی در فولاد SPK که تحت عملیات حرارتی قرار گرفته نشان میدهد که توزیع یکنواختتر کاربیدهای اولیه در فولاد SPK قبل از عملیات حرارتی باعث شده که این فولاد استحکام خمشی به مراتب بهتری را در دماهای مختلف تمپر از خود نشان دهد. دلیل کاهش استحکام این نوع فولاد پس از عملیات تمپر ناشی از وجود کاربیدهایی است که شدت تنش در اطراف آنها زیاد بوده و در نهایت منجر به جوانهزنی و رشد ترک میشوند.
در همین راستا گزارش شده است که فولادهای ابزار کارسرد با کاربیدهای کروی نسبت به آنهایی که کاربیدهای شبکهای دارند، استحکام ضربهای، چقرمگی شکست و مقاومت بیشتری را در مقابل جوانهزنی ترک خستگی از خود نشان میدهند.